Commonly used battery products
(1) Power lithium secondary battery (such as electric vehicle battery, electric bicycle
driving battery, electric tool battery, etc.)
(2) Lithium secondary batteries for mobile communication products (such as mobile phone batteries,
Cordless phone batteries, Bluetooth headset batteries, walkie-talkies, etc.)
(3) Lithium secondary batteries for portable products (such as laptop batteries
battery, PDA battery, camera battery, video camera battery, recording
Pen batteries, game console batteries, e-book batteries, etc.)
(4) Various primary batteries (such as lithium-manganese batteries, lithium-sub-batteries, lithium
iodine battery, lithium-sulfur battery, etc.)
Lithium-ion battery: lithium metal battery (metal lithium directly and reaction, disposable batteries), lithium-ion batteries (lithium ions in the positive and negative
Working back and forth between, is a secondary battery (rechargeable battery))
Li-ion battery key material
Positive electrode material - the active material is generally lithium manganese oxide or lithium cobalt oxide, nickel cobalt lithium manganese oxide material, electric bicycle
Nickel cobalt lithium manganate (commonly known as ternary) or ternary + a small amount of lithium manganate, pure lithium manganate and iron phosphate are generally used
Lithium is gradually fading out due to its large size, poor performance or high cost. Conductive current collectors use a thickness of 10-20 microns
meters of electrolytic aluminum foil.
u Diaphragm—a specially shaped polymer film with a microporous structure that allows lithium ions to pass freely
pass, but electrons cannot pass.
u Negative electrode material - the active material is graphite, or carbon with a similar graphite structure, and the thickness of the conductive current collector is
7~15 micron electrolytic copper foil.
u Organic electrolyte—a carbonate-based solvent dissolved in lithium hexafluorophosphate, and a gel-like electrolyte for polymers
liquid.
u Battery casing——divided into steel casing (square type is rarely used), aluminum casing, nickel-plated iron casing (used for cylindrical battery),
Aluminum-plastic film (soft packaging), etc., as well as the cap of the battery, are also the positive and negative terminals of the battery.
Battery Separator Inspection - Thickness
Thickness detection: The thickness of the lithium battery separator is not uniform, and the liquid retention capacity and electronic insulation are reduced, which will adversely affect the battery performance. for preparation
A battery separator with higher comprehensive performance requires precise thickness testing to ensure that the uniformity and thickness of the battery separator meet the standards.
Battery Separator Testing - Film Heat Shrinkage Properties
Thermal shrinkage properties of the film: Since the diaphragm is prone to shrinkage and deformation at high temperatures, it can be characterized by the thermal shrinkage rate of the diaphragm at high temperature.
dimensional stability. For lithium-ion battery separators, the thermal shrinkage rate should be less than 5% when placed at 90°C for 60 minutes. hot harvest
The shrinkage rate is low, which can prevent thermal runaway caused by short circuit of positive and negative poles.
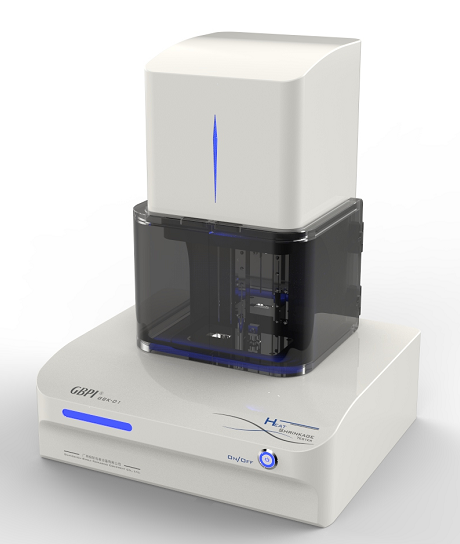
For more information about lithium battery testing solutions, please contact us directly